BECx: How Will Your Building Envelope Actually Perform?
We design building envelopes to be efficient, but do we know how they’ll actually perform?
This is one of the many questions we get as the building industry’s focus moves towards more aggressive energy efficiency targets including Net Zero Energy and Passive House. With these new targets the attention is starting to now shift to one of the often overlooked energy systems of a building – the Passive Energy system – also known as the building envelope.
This focus on Passive Energy is where Building Envelope Commissioning (BECx) can provide value to a project. BECx is much more than just testing, or achieving the ever-valuable 2 points in LEED v4 projects. When effectively implemented it can be a critical process in realizing your high performance requirements, while also reducing risks of future envelope performance issues.
Before You Start, Know Your Goals
The BECx process starts with ensuring you have a clear set of Owner’s Project Requirements (OPR) which outlines everything the Owner wants – including building performance goals. The envelope performance aspects should, at minimum, include goals related to water penetration, condensation, air leakage, and thermal performance/energy. The OPRs will help guide designers and identify areas of high priority early in the design process, making the project more likely to meet the performance goals.
Verification Testing: Timing is Critical
While the performance of most Active systems (mechanical and electrical systems) is confirmed after installation or ‘fine tuned’ on site, the opposite should occur for the building envelope.
You want to focus more on the critical areas of the building envelope during design through design reviews and modeling, then during construction use the mock-up, observations, and finally site testing as a means to confirm the performance. This installation verification is key, as the ability to make any adjustments after envelope completion is limited, disruptive to the schedule and can be very expensive. There is nothing worse than having to tear-out and reinstall glazing because it wasn't mocked-up and tested early in the installation.
There are many innovative strategies available that can be used to accompany the BECx process, including quantitative analysis and 3D modeling, which help to better predict the envelope's actual performance for factors such as potential for condensation, interior surface temperature, and heat loss.
There’s Value in Experience
Even though testing is part of the BECx process, it isn’t the only OPR verification tool when it comes to your building’s Passive Energy system. The value that hands-on experience can bring to a project should not be overlooked.
Engaging an experienced BECx professional on your project can help, as they will have knowledge from previous projects and can provide insight regarding what works and what doesn’t. They will know the correlation between the details and materials, and how the assemblies will actually perform on the project.
Have questions about the BECx process or how a Building Envelope professional can help your project? Reach out to us! We’d be happy to chat with you.
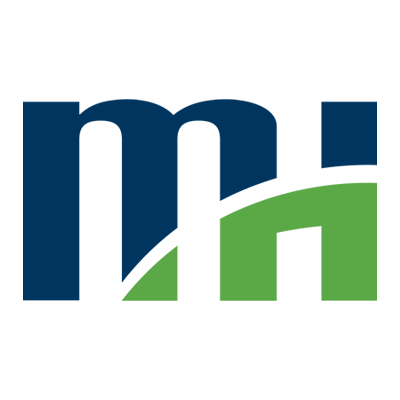
Posts by Topic
Topics
- 5G (1)
- ACEC (3)
- Active Transportation (5)
- AFP/P3 (6)
- Alberta (5)
- Anniversary (1)
- approvals (1)
- Architect (2)
- Atlanta (2)
- Awards (62)
- Biophysical Sciences (1)
- Board of Directors (1)
- Bridge Rehabilitation (3)
- Building and Facilities Engineering (2)
- Building Energy (25)
- Building Envelope (48)
- Building Science (65)
- Calgary (2)
- Canada 150 (1)
- Canstruction (2)
- Capabilities (1)
- Carbon emissions (2)
- Carbon Pathfinder Tool (1)
- Carson Awards (5)
- Charity (13)
- Climate Adaption (7)
- climate change (7)
- Code and Life Safety (8)
- Commercial Buildings (4)
- Commissioning (11)
- Construction (2)
- Construction Administration (5)
- Consulting Engineering (1)
- Critical Facilities (33)
- CSR (24)
- Culture (5)
- Dallas (1)
- Data Center (22)
- Data Center Commissioning (9)
- Data Center Design (12)
- design (9)
- Design Build (1)
- DSSP (1)
- edgecomputing (1)
- edgetechnologies (1)
- Edmonton (4)
- Electrical (24)
- Electrical engineering (8)
- Energy (8)
- Engineers Canada (5)
- Environmental (36)
- Environmental Compensation (1)
- Environmental Impact Assessment (3)
- environmental planner (3)
- Environmental Planning (5)
- ETFE (1)
- Event (12)
- Existing Buildings (6)
- Facade Engineering (4)
- Ferry Docks (2)
- FIDIC (3)
- fisheries biologist (1)
- Flood Mapping (1)
- Florida (1)
- Forensic Investigation (1)
- Fundraising (11)
- garage (2)
- Gender Diversity (8)
- Gender Intelligence (3)
- Geometric Design (2)
- Government (14)
- Hospitality (1)
- Houston (4)
- Hydro (2)
- India (1)
- industrial (4)
- Infrastructure (28)
- Innovation (1)
- interchange (1)
- IWD (2)
- IWD2021 (1)
- Land Development (8)
- Landfill (4)
- Manitoba (1)
- MCF (3)
- Mechanical (21)
- Mechanical Engineering (1)
- MEP (1)
- mission critical (10)
- Moncton (1)
- Motivational MH'er (1)
- Multi-Use Pathways (1)
- Municipal Infrastructure (5)
- municipal solid waste (2)
- MUP (1)
- New Brunswick (1)
- New Hire (17)
- New Role (3)
- Newsroom (121)
- northern communities (2)
- NVTC (2)
- ontario (1)
- Operations Consulting (8)
- Ottawa (2)
- Panel (3)
- People (124)
- Project Management (6)
- QAP (1)
- Rail (1)
- Reconstruction (1)
- regulatory (1)
- Renewable Energy (2)
- resiliency (3)
- Risk Management (1)
- Roads and Highways (3)
- Salt Lake City (1)
- Seattle (1)
- Security (4)
- Social Responsibility (30)
- Solid Waste (11)
- solid waste management (5)
- St Johns (2)
- Stantec (1)
- Structural (14)
- Sustainability (23)
- Telecom (9)
- Texas (1)
- Toronto (13)
- towers (1)
- Traffic Assessment (2)
- Transfer Station (1)
- Transit (13)
- Transit Consultant (3)
- Transit Infrastructure (3)
- Transit Planning (2)
- Transportation (30)
- Transportation Engineering (8)
- transportation structures (2)
- TTC (1)
- Vancouver (6)
- Virginia (2)
- Washington DC (3)
- Waste to Energy (2)
- Water & Wastewater (8)
- Water Resources (3)
- wellfield (1)
- wellness challenge (1)
- Whistler (1)
- Whitehorse (1)
- Wireless (2)
- Women in Engineering (5)
- Yukon (5)